Table of content
Ask
A physical device measures the ripeness of the fruits and sends the relevant data about the fruit ripening process automatically to a digital platform where the data is collected, united and analysed. With this data, core processes in the supply and distribution chain can be optimised and improved. Experience Fruit Quality uses Artificial Intelligence in their data modelling to extract relevant insights.
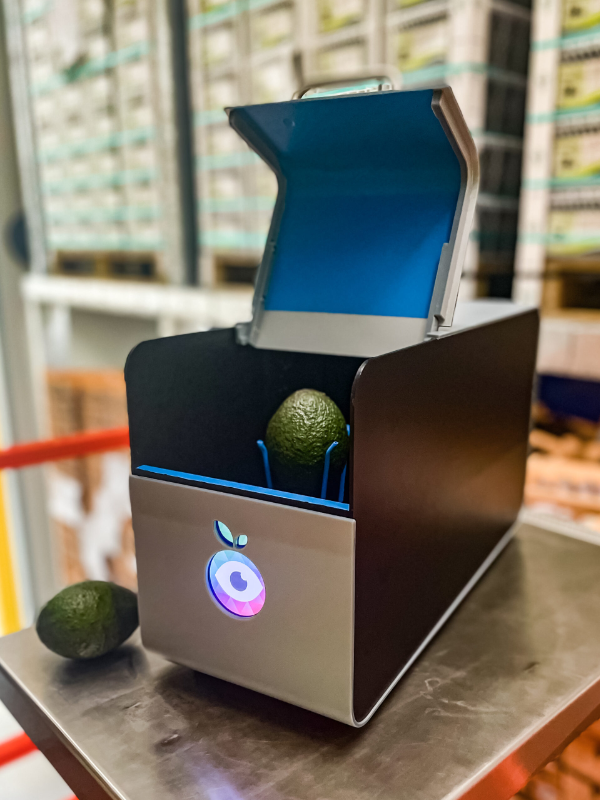
Because the fruits stay fully intact during the measuring process instead of being cut and manually assessed, less fruits are being compromised and waste is minimised. Making this a non-destructive and more sustainable process.
Experience Fruit Quality asked us to help translate the complexity of the tool and the data derived from their clients' businesses into a comprehensible digital dashboard that is usable in the day-to-day decision making of their clients.
Answer
Experience Fruit Quality’s goal is to collect all the relevant data sources and ripening results of the fruit in one place throughout the entire supply chain of avocados or mango ripening processes.
For this reason, we proposed a redesign of the interface platform from a human centred point of view. We wanted to:
- Make sure the different locations and production steps in the journey of the fruit pallets were made explicit, so to track the ripening process;
- Support the operators in their daily responsibility of the fruits and make sure they have a grip on the specific actions that need to be handled during this journey.
→ Want to fully understand your user’s experience? Read “From shadowing sessions to action points: Customer Journey Mapping at fresk.digital”.
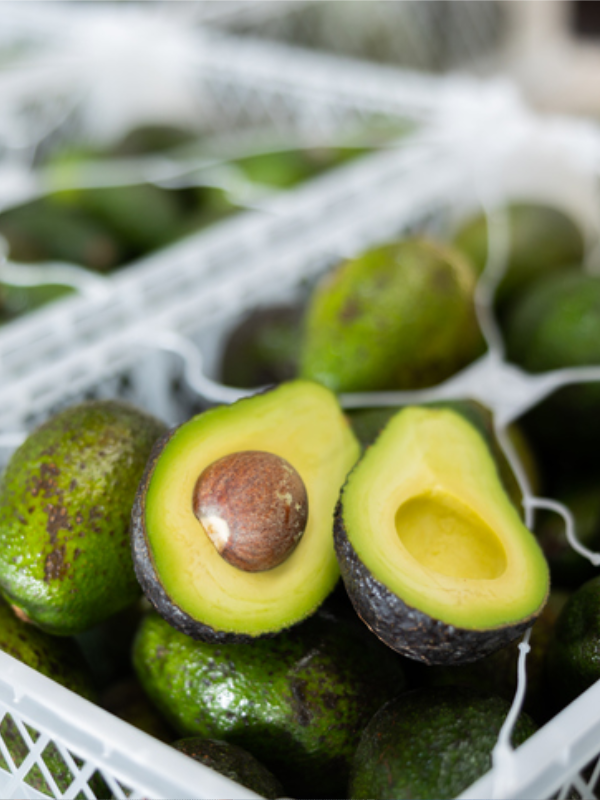
Way of working
During the Discovery phase, we have analysed the usability of the existing flow from a user point of view. We have then collected all the possible bottlenecks and translated them into needs for the redesign, starting from a new and user centred flow.
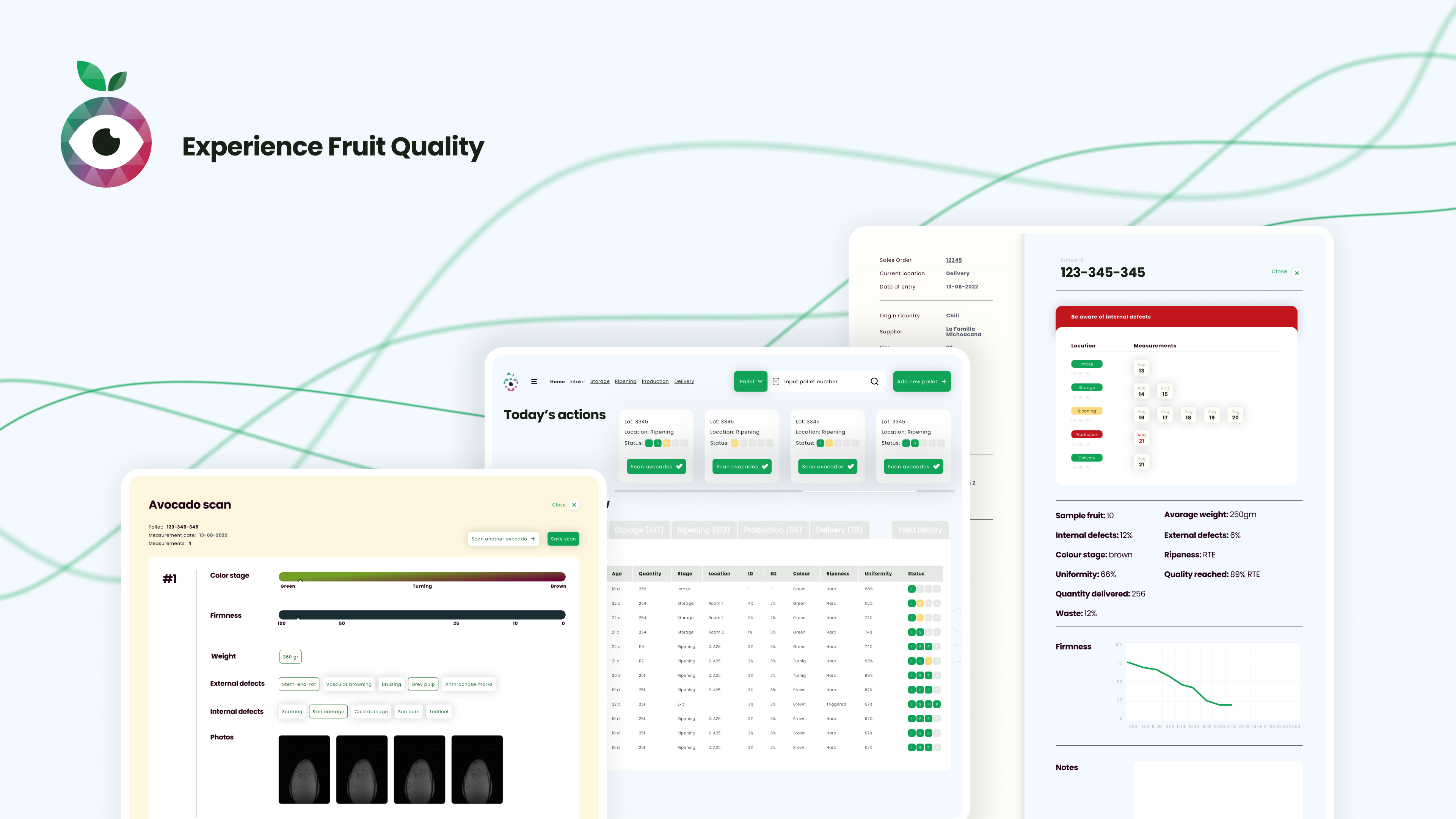
During the Strategise phase we have translated the needs into an interactive prototype, using an iterative process to come to the final prototype: the prototype has been tested and checked internally by EFQ employees on a weekly basis in order to understand if the flow and features were matching the end goals.
{{Quote-component}}
Result
In a great partnership with our client we were able to deliver an interactive prototype that organises the experience in 3 different layers of interaction:
- The homepage gives the full overview of all the pallets present, and functions as a starting point for a deep dive into more details.
- Detailed paginas where the specific measurements.
- Summaries of data are collected in a visual pleasing and usable way.
This provides the overview and focus in one platform which supports the operators in their day-to-day handling of the fruit pallets. This empowers them in their decision making, because they are continuously presented with all relevant data to help them in their choices.
Heading
Lorem ipsum dolor sit amet, consectetur adipiscing elit. Suspendisse varius enim in eros elementum tristique. Duis cursus, mi quis viverra ornare, eros dolor interdum nulla, ut commodo diam libero vitae erat. Aenean faucibus nibh et justo cursus id rutrum lorem imperdiet. Nunc ut sem vitae risus tristique posuere.
"The fresk.digital team managed to apply a human centered approach to our data driven solution, and the synergy created is going to make this process sustainable and more valuable."
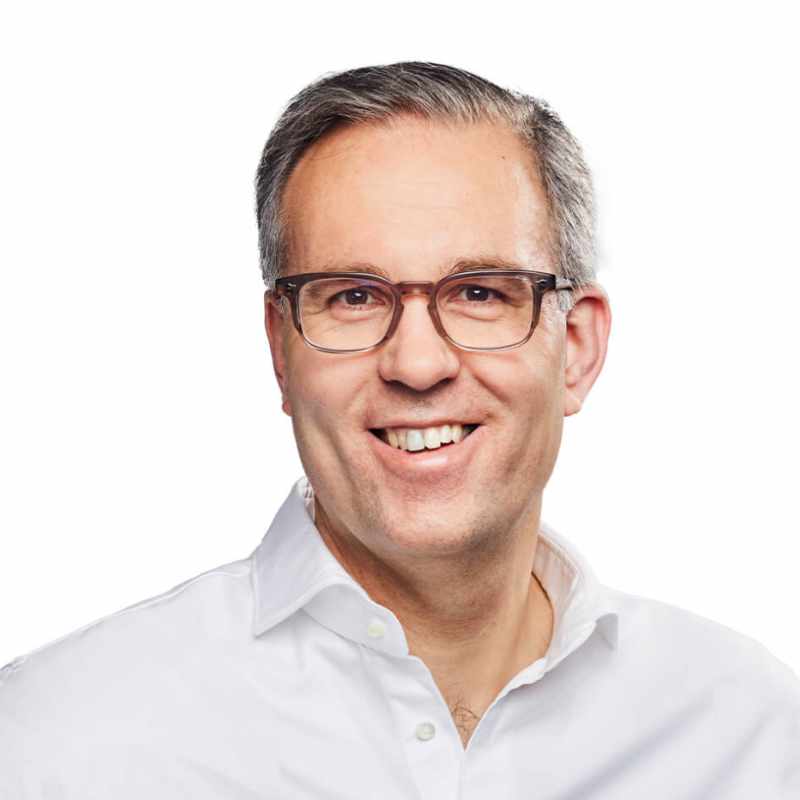